How To Calculate Creep In Printing
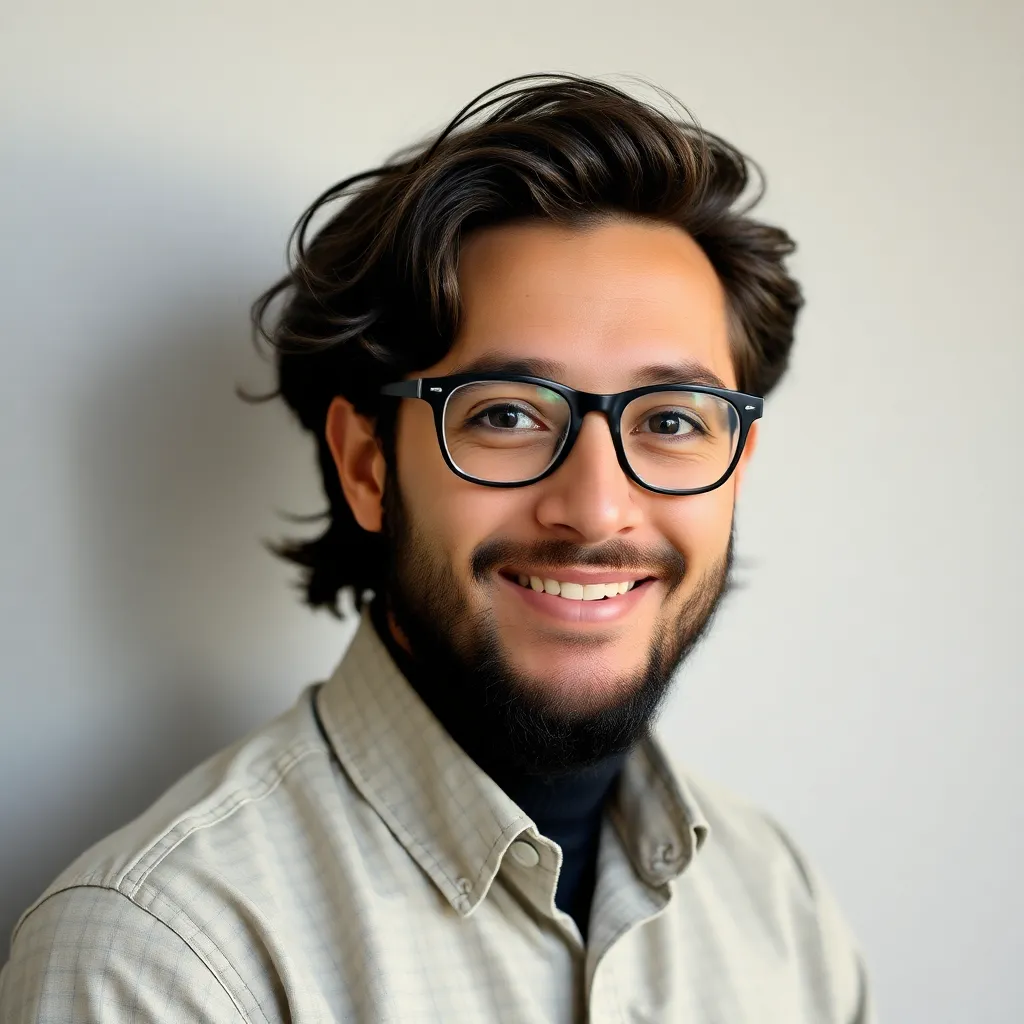
Ronan Farrow
Mar 03, 2025 · 3 min read

Table of Contents
How to Calculate Creep in Printing: A Comprehensive Guide
Creep, in the context of printing, refers to the gradual dimensional change of a printed material over time. This is especially crucial in applications requiring precise dimensions and long-term stability, such as packaging, labels, and precision electronics. Understanding and calculating creep is essential for ensuring print quality and preventing costly errors. This guide will break down how to calculate creep in printing, focusing on practical applications and considerations.
Understanding the Factors Influencing Creep
Before delving into calculations, let's establish the key factors influencing creep in printed materials:
1. Material Properties:
- Substrate Type: Different substrates (paper, plastic films, textiles, etc.) exhibit varying degrees of creep. The inherent properties of the material, like its elasticity and molecular structure, significantly impact its propensity to creep. Paper, for example, is more susceptible to creep than some plastic films.
- Ink Type: The ink used also plays a role. Certain inks might plasticize the substrate, increasing creep, while others have minimal effect. Solvent-based inks are generally known to cause more creep than water-based inks due to their interaction with the substrate.
- Coating: Coatings applied to the substrate can influence creep. Some coatings add stiffness, reducing creep, while others might have the opposite effect.
2. Environmental Factors:
- Temperature: Higher temperatures generally accelerate creep. The molecular movement within the material increases at higher temperatures, leading to greater dimensional changes.
- Humidity: Humidity can significantly affect creep, particularly in materials sensitive to moisture absorption. High humidity can soften some materials, increasing creep.
- Stress: The amount of stress placed on the printed material will directly influence the amount of creep observed. Higher stress levels generally result in more significant creep.
3. Printing Process:
- Drying Time: Insufficient drying time can lead to increased creep due to the continued movement of ink and solvent within the material.
- Pressure: The pressure applied during printing can also affect the material and induce creep, especially in certain substrates.
Calculating Creep: A Practical Approach
Precisely calculating creep is complex and often requires specialized equipment and software. However, a simplified approach for practical purposes involves measuring dimensional changes over time.
Here's a step-by-step guide:
- Sample Preparation: Prepare several identical samples of your printed material. Ensure consistent printing conditions across all samples.
- Initial Measurement: Accurately measure the dimensions (length, width, etc.) of each sample using precise measuring instruments (calipers, micrometers).
- Controlled Environment: Store the samples in a controlled environment with constant temperature and humidity. This is crucial for consistent and accurate results.
- Periodic Measurement: At predetermined intervals (e.g., daily, weekly, monthly), re-measure the dimensions of each sample.
- Data Analysis: Calculate the percentage change in dimensions for each sample at each measurement interval. This involves subtracting the initial measurement from the subsequent measurements, dividing by the initial measurement, and multiplying by 100%.
- Creep Rate Determination: Plot the percentage change in dimensions against time. This will give you a visual representation of the creep rate. The slope of the curve provides an indication of the creep rate.
Minimizing Creep in Printing
While complete elimination of creep is often impossible, you can minimize it through several strategies:
- Substrate Selection: Choose substrates known for low creep properties.
- Ink Optimization: Select inks with minimal interaction with the substrate.
- Controlled Drying: Ensure adequate drying time under controlled conditions.
- Environmental Control: Maintain stable temperature and humidity during printing and storage.
- Improved Printing Techniques: Optimize printing parameters, such as pressure, to minimize stress on the printed material.
By understanding the factors influencing creep and employing appropriate mitigation strategies, printers can improve the quality and longevity of their printed products. Remember that the method described above is a simplified approach. For precise calculations and in-depth analysis, consulting material science specialists and using advanced testing equipment is recommended.
Featured Posts
Also read the following articles
Article Title | Date |
---|---|
How Long Do Sealants Last | Mar 03, 2025 |
How Does Fixing Our Mental Health Improve Our Love Language | Mar 03, 2025 |
How To Increase Cute Ftp View Font Windows | Mar 03, 2025 |
How Do You Bleed The Clutch Master Cylinder | Mar 03, 2025 |
How To Nrepair Code U110b 0n A 09 Mercedes E350 | Mar 03, 2025 |
Latest Posts
-
How To Style Maxi Dress For Fall
Apr 16, 2025
-
How To Style Huaraches
Apr 16, 2025
-
How To Style An A Line Dress
Apr 16, 2025
-
How To Style A Utility Jacket
Apr 16, 2025
-
How To Style A Line Dress
Apr 16, 2025
Thank you for visiting our website which covers about How To Calculate Creep In Printing . We hope the information provided has been useful to you. Feel free to contact us if you have any questions or need further assistance. See you next time and don't miss to bookmark.