How To Make Refractory Cement
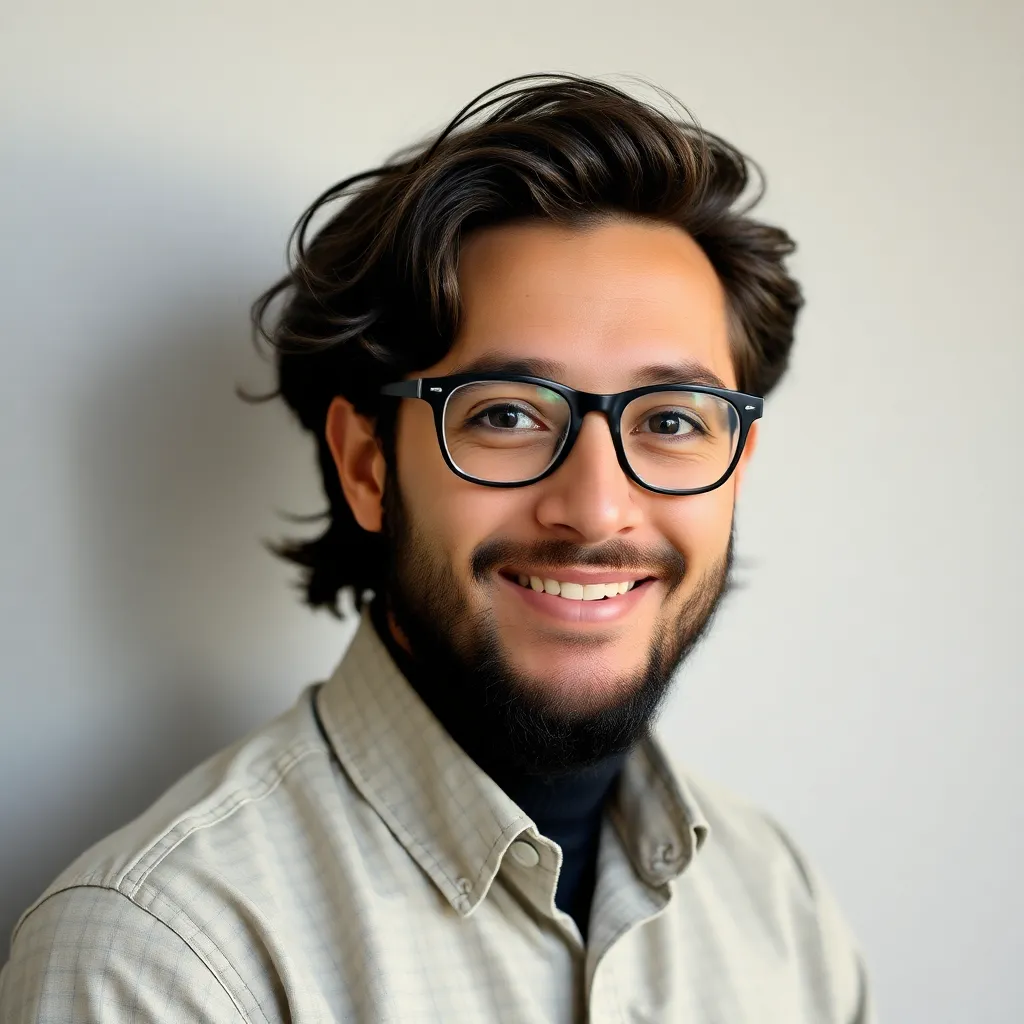
Ronan Farrow
Mar 25, 2025 · 3 min read
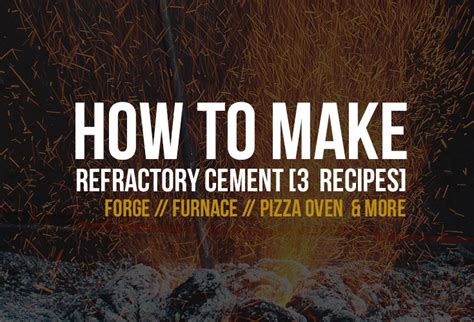
Table of Contents
How to Make Refractory Cement: A Comprehensive Guide
Refractory cement is a specialized material used in high-temperature applications, providing excellent heat resistance and durability. Knowing how to make it can be incredibly valuable for various projects, from repairing firebricks in a fireplace to creating custom high-temperature components. This guide will walk you through the process of making refractory cement, covering the essential ingredients and steps involved. Remember, safety is paramount when working with high-temperature materials; always wear appropriate protective gear.
Understanding Refractory Cement
Before diving into the process, it's crucial to understand what makes refractory cement special. Unlike standard cement, refractory cement can withstand extremely high temperatures without significant degradation. This is achieved through the use of specific refractory aggregates and binders that are resistant to thermal shock and chemical attack.
Key Properties of Refractory Cement:
- High-Temperature Resistance: This is the core characteristic, allowing it to withstand temperatures far exceeding those that would damage ordinary cement.
- Chemical Inertness: It resists chemical reactions and degradation even under harsh conditions.
- Low Thermal Expansion: This prevents cracking or crumbling due to temperature fluctuations.
- Strength and Durability: Refractory cement must possess sufficient strength to withstand the stresses of high-temperature applications.
Ingredients for Making Refractory Cement
The specific recipe for refractory cement depends on the desired application and the temperature it will endure. However, common ingredients include:
-
Refractory Aggregate: This forms the bulk of the cement and dictates its heat resistance. Common aggregates include alumina, silica, zirconia, and other high-temperature resistant materials. The size and type of aggregate will impact the final properties of your cement. Fine and coarse aggregates are often combined for optimal strength and workability.
-
Refractory Binder: This binds the aggregate together and provides cohesion. Common binders include calcium aluminate cement, sodium silicate, or other specialized high-temperature binders. The choice of binder will significantly influence the setting time and ultimate strength of the cement.
-
Water: Water is essential for the hydration and setting process of the cement. The amount of water used will impact the workability and consistency of the final product. Too much water can weaken the cement, while too little will make it difficult to work with.
Steps to Make Refractory Cement
While specific ratios will vary based on the desired properties, the general process remains consistent:
1. Preparation:
- Gather your ingredients: Ensure you have the correct amounts of refractory aggregate (both fine and coarse), refractory binder, and clean water.
- Dry Mixing: Thoroughly mix the dry refractory aggregate and binder in a clean, dry container. This ensures even distribution of the binder throughout the mixture.
2. Adding Water:
- Gradual addition: Slowly add water to the dry mixture while continuously mixing. Avoid adding too much water at once.
- Mixing consistency: Mix until a workable paste or slurry is formed. The consistency should be similar to that of regular mortar.
3. Application:
- Immediate application: Refractory cement typically has a relatively short working time. Apply the cement immediately after mixing.
- Proper techniques: Use appropriate techniques for your specific application (e.g., troweling, packing, etc.).
4. Curing:
- Controlled curing: Allow the cement to cure properly. This usually involves maintaining a specific temperature and humidity to allow for proper hydration and hardening. The curing process can influence the final strength and durability of the refractory cement. Refer to the instructions of your specific binder for detailed curing requirements.
Safety Precautions
Working with refractory materials requires caution:
- Respiratory protection: Always wear a respirator to avoid inhaling dust.
- Eye protection: Wear safety glasses to protect your eyes from flying particles.
- Gloves: Use protective gloves to avoid skin irritation.
- Proper ventilation: Work in a well-ventilated area.
Making refractory cement is a specialized process. This guide offers general instructions; always refer to the specific instructions provided with your chosen ingredients for optimal results and safety. Remember, experimenting with different ratios and types of ingredients may be necessary to achieve the desired properties for your particular application.
Featured Posts
Also read the following articles
Article Title | Date |
---|---|
How To Pre Order Jordans | Mar 25, 2025 |
How To Install Cumination On Firestick | Mar 25, 2025 |
How To Remove Sand From Pool Bottom | Mar 25, 2025 |
How To Remove Tint Adhesive From Window | Mar 25, 2025 |
How To Play Cypress Point | Mar 25, 2025 |
Latest Posts
-
How Long After A Chiropractic Adjustment Can I Workout
Apr 05, 2025
-
How Long After A Cartilage Piercing Can You Swim
Apr 05, 2025
-
How Long After A Brow Lamination Can I Shower
Apr 05, 2025
-
How Late Is Too Late For A Date
Apr 05, 2025
-
How Late Can You Plant Sunflowers Zone 5
Apr 05, 2025
Thank you for visiting our website which covers about How To Make Refractory Cement . We hope the information provided has been useful to you. Feel free to contact us if you have any questions or need further assistance. See you next time and don't miss to bookmark.